Standing seam system
The standing seam system makes it possible for a zinc roof or façade to be covered with titanium zinc quickly and at reasonable cost. This is because preformed bays are used, and the seams are folded mechanically, reducing manual folding to a minimum. The preformed bays are supplied in custom-made sizes and are locked together on site with a single or double fold, by machine or by hand. Aside from straight bays, curved (convex and concave) and tapering bays can be made without problems. The bays are secured to the substructure by means of fi xed and sliding clips (see figure 6.1.4).
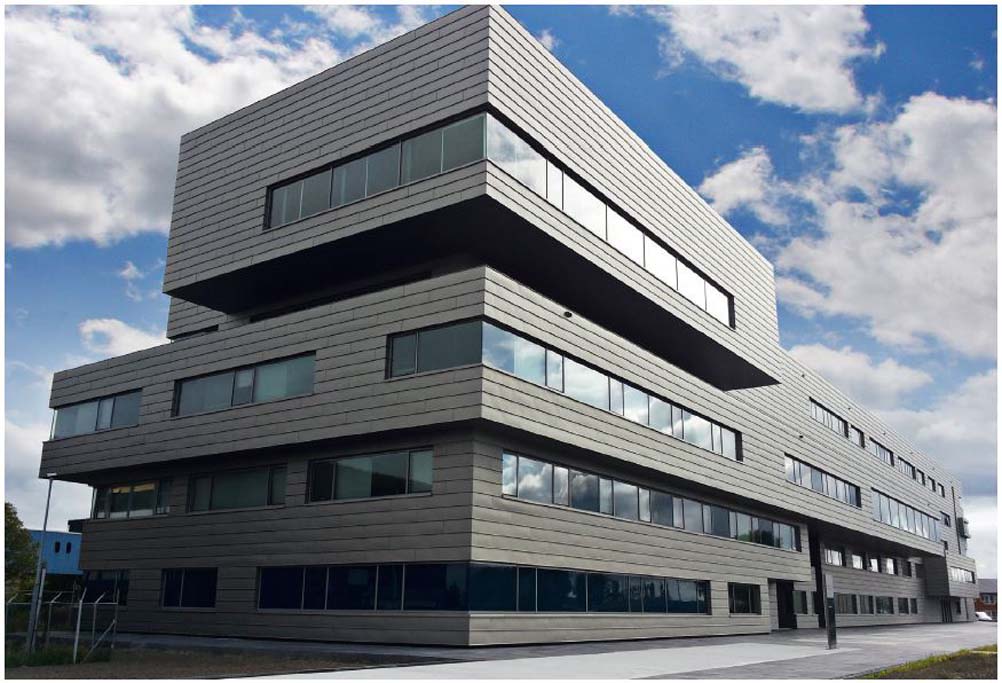
The standing seam system for façades
With a standing seam façade, the zinc bays are connected in the longitudinal direction with so-called standing seams. The material thickness is 0.80 mm. The allowable bay width is determined by the wind load and the height of the façade. If the standing bay installed horizontally, then it is recommended to limit the bay width to 300 to 430 mm for optimal work, and to limit the length to about 5 meters for handling reasons. If the standing seam bays are installed vertically, then limiting the bay width to 500 mm or less and the bay length to about 6 meters is recommended for handling reasons. The sheets are connected with a single clip at the top end.
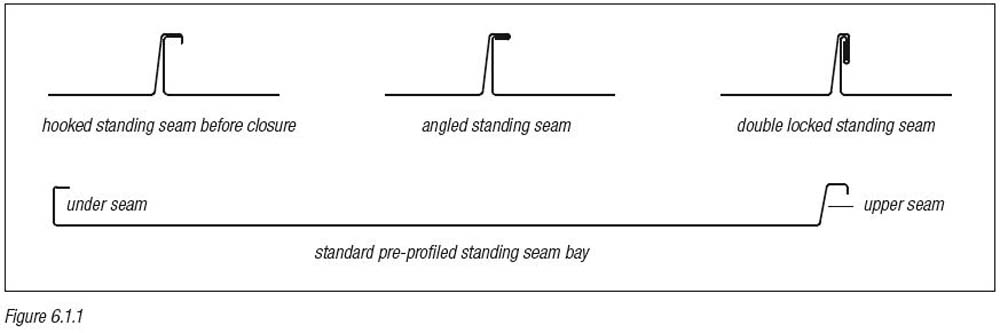
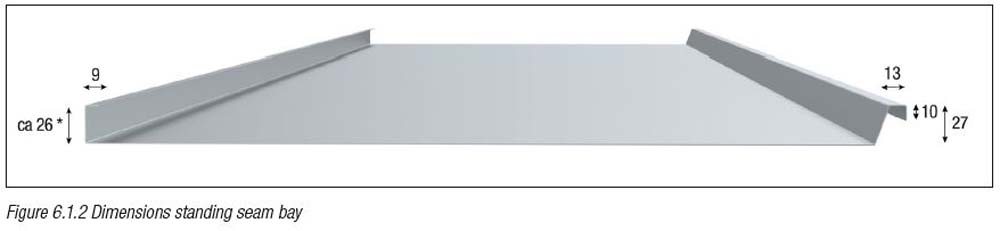
To promote the rain proofi ng aspect of a standing seam façade, sealing tape can be affi xed between the seams. This is also recommended for unventilated systems that pose a risk of leakage.
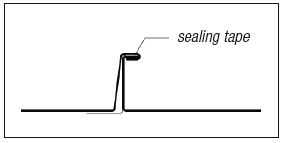
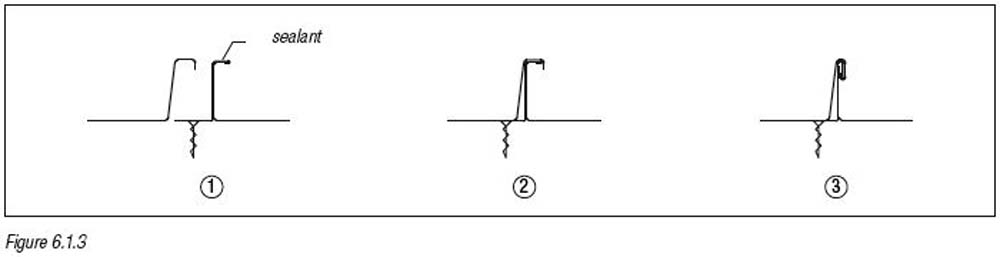
Fastening the clips
The bays are secured to the substructure by means of fi xed and sliding clips (see figure 6.1.4).
The fixed clips secure the standing seam bay and the sliding clips make longitudinal expansion possible. The clip is secured over the lowest standing seam bay and on the sub construction. Then the top standing seam bay is placed over this and folded shut.
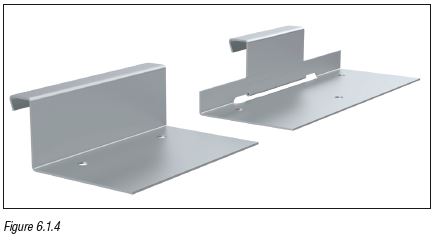
Support
The standing seam system must be fully supported by unplaned, untreated wooden boards at least 23 mm thick, not tongue and grooved, with gaps of at least 5 mm and maximum 100 mm. The construction requirements are also important in this. Use galvanised nails with a zinc-layer thickness of at least 20 microns or AISI 304 stainless steel for fastening.