Zinc standing seam system
The standing seam system provides a rain-tight roof and façade covering where the angle of inclination is in excess of 3°, preferably > 7°. The single standing seam is used for roofs with an angle of inclination steeper than 25° and for façades. For a zinc roof with a pitch angle lower than 25° the double standing folded seam is used.
The standing seam system makes it possible for a roof or façade to be covered with titanium zinc quickly and at reasonable cost. This is due to the fact that prefabricated panels, and the seams are folded mechanically, reducing manual folding to a minimum. The prefabricated panels are supplied in custom-made sizes and are locked together on site with a single or double fold, by machine or by hand. Aside from straight panels, curved (convex and concave) and tapering bays can be made easily. The bays are secured to the substructure by means of fixed and sliding clips (see figure 5.1.1).
See also:
Ventilated roof built up standing seam system
Damp proof roof built up with standing seam system
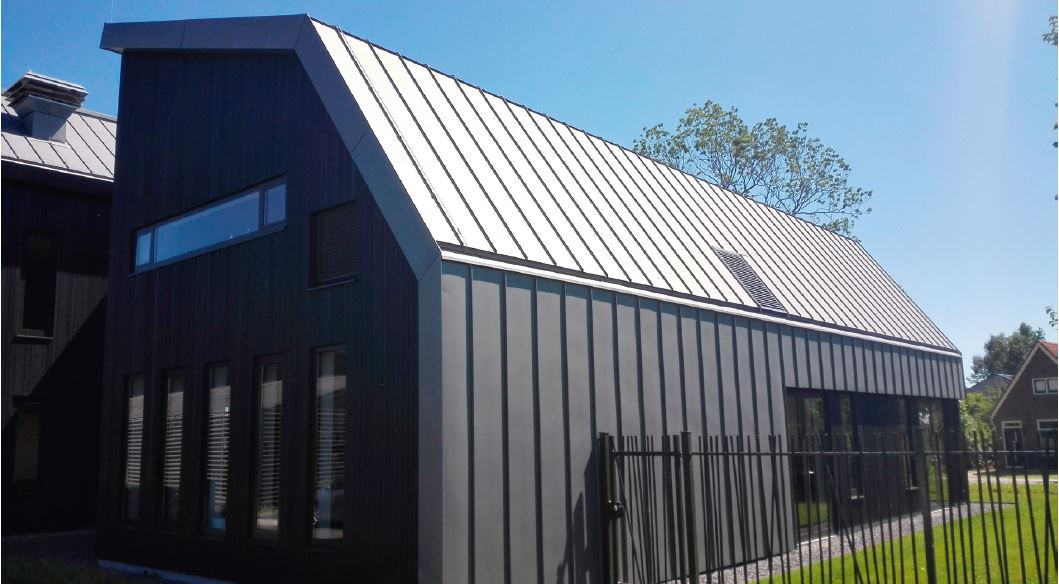
Standing seam cladding
With a standing seam roof, the zinc bays are joined together lengthwise with so-called (double) standing seam. The material thickness is 0.80 mm. The allowable bay width is determined by the wind load and the height of the roof. The advised bay width varies from 330 mm to 530 mm. The advised maximum bay length is 10 meters (thermal movement: 20 mm). When making a selection, consider the ease of handling.
The standing seam can consist of a single or double connection. A single connection forms a less effective water seal and may therefore only be used on roofs with a pitch angle larger than 25°. With fixed clips the standing seam cladding is fixed over a one-meter length. Sliding clips are used for the remaining length of the roof bay. The location of the fixed clips depends on the pitch angle of the roof. The relationship between the location of the fixed clip and the pitch angle is shown in figure 5.1.6. Fixed clips ensure that the standing seam panels don’t slip. Panels up to 3 meters long can be fully secured with fixed clips. For lengths greater than 3 meters the bay is secured with fixed clips over a length of one meter, and the rest with sliding clips.
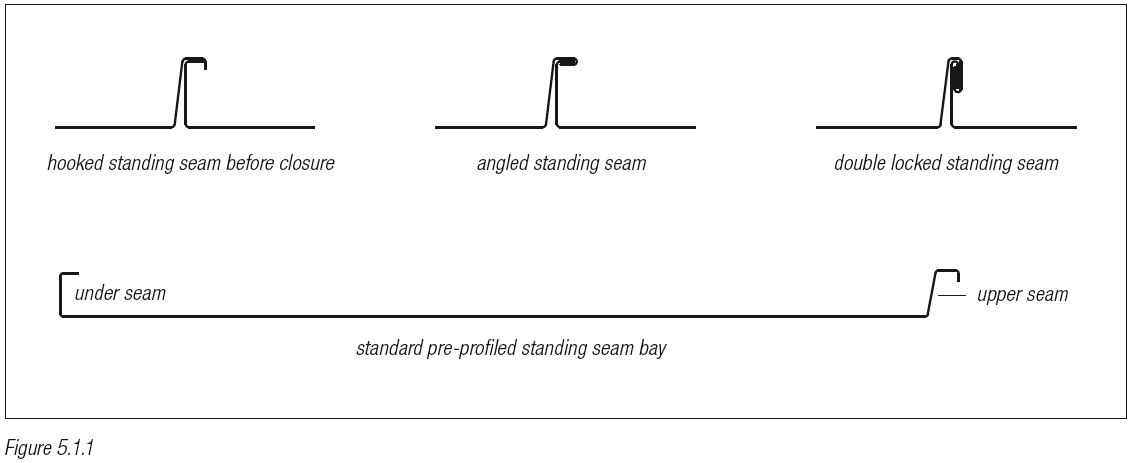
Standing seam
The standard height of a standing seam for a profiled seam is 25 mm. A seam height of 38 mm is sometimes used to accentuate shadow formation. The higher seam also offers improved rain proofing in the case of windy conditions.
To promote the rain proofing aspect of a standing seam roof, sealing tape can be affixed between the seams. This is also recommended for unventilated systems that pose a risk of leakage.
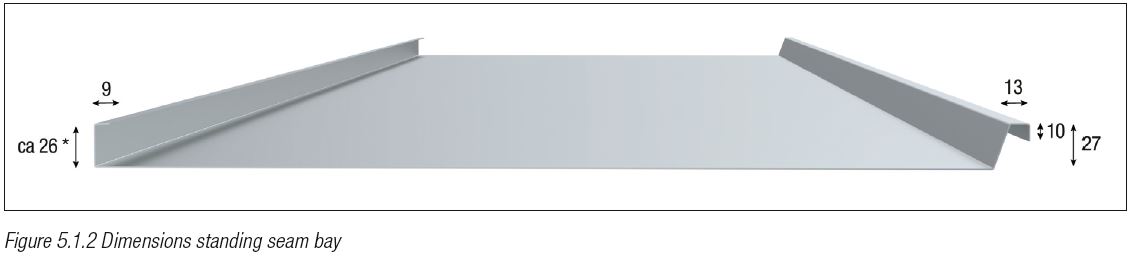
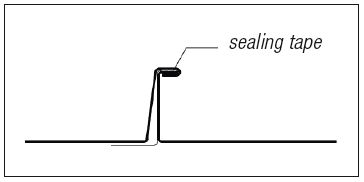
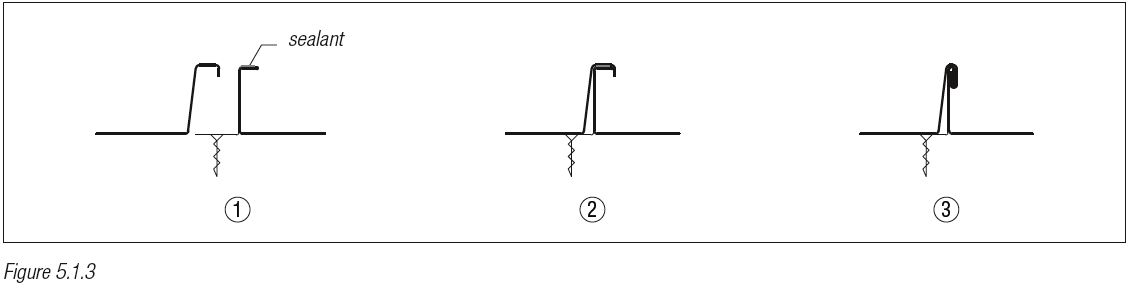
Fastening the clips
The bays are secured to the substructure by means of fixed and sliding clips (see figure 5.14, fixed and sliding clip). The fixed clips secure the standing seam bay and the sliding clips make longitudinal expansion possible. The clip is secured over the lowest standing seam bay and on the sub-construction. Then the top standing seam bay is placed over this and folded shut.
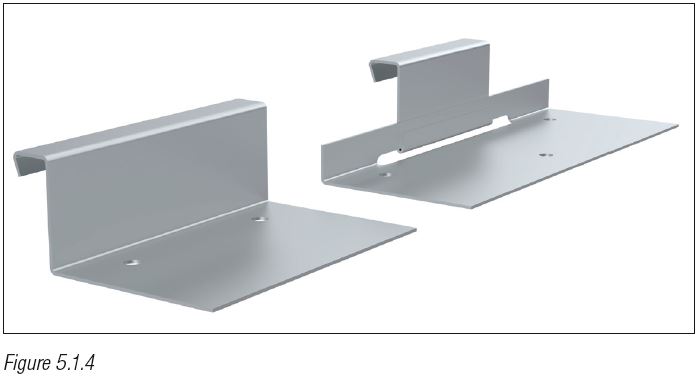
Support of a zinc standing seam system
The standing seam system must be fully supported by unplaned, untreated wooden boards at least 23 mm thick, not tongue and grooved, with gaps of at least 5 mm.
The space between the boards can be larger depending on the pitch of the roof, i.e.
- roof pitch up to 45º 5 – 10 mm
- roof pitch from 45º – 70º 5 – 50 mm
- roof pitch from 70º – 90º 5 – 100 mm
The construction requirements are also important in this. Use galvanized nails with a zinc-layer thickness of at least 20 microns or AISI 304 stainless steel for fastening.
Standard details
Below are some examples of typical details for roofing. These details outline the standard situation and serve as a guideline for applying the standing seam system on roof structures.
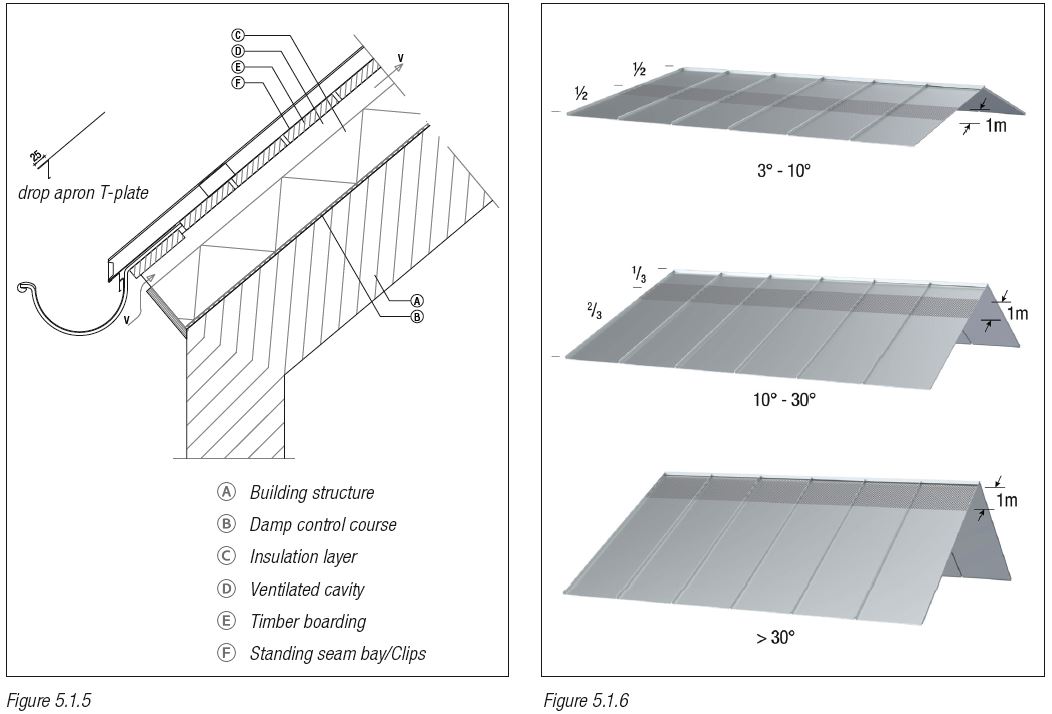
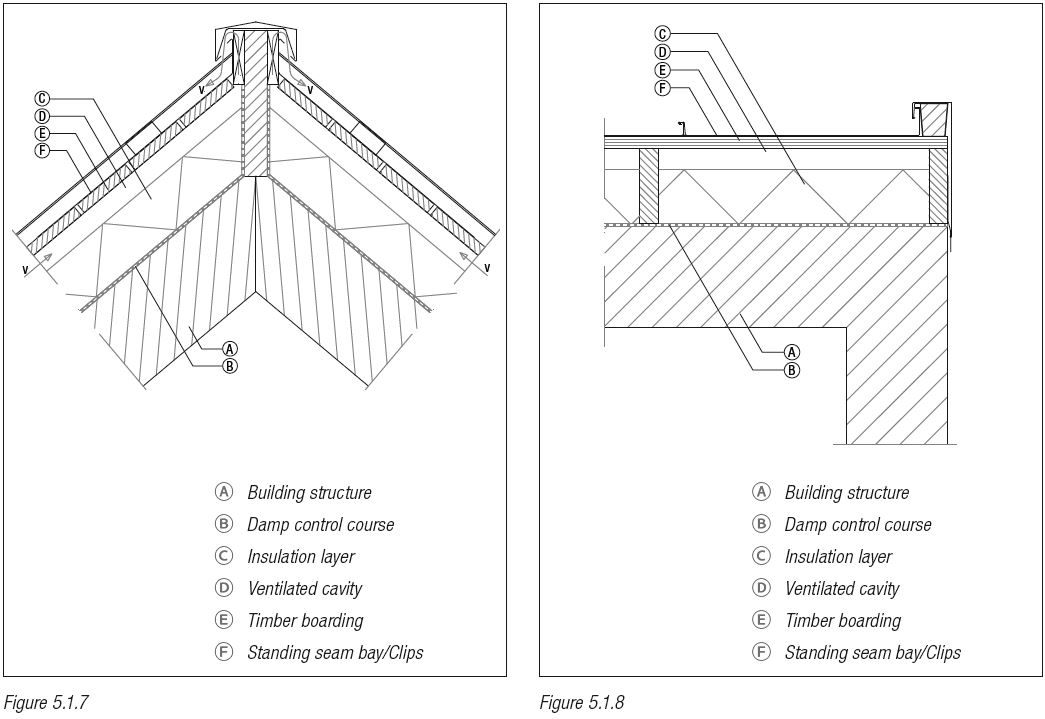
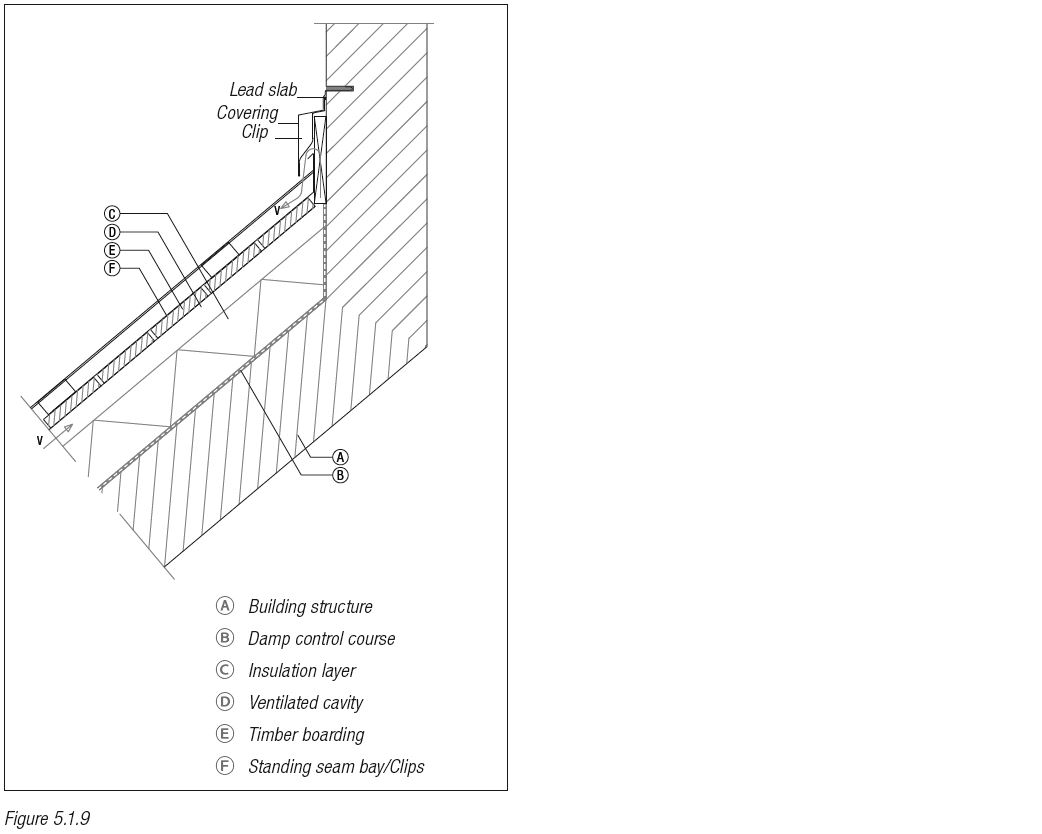
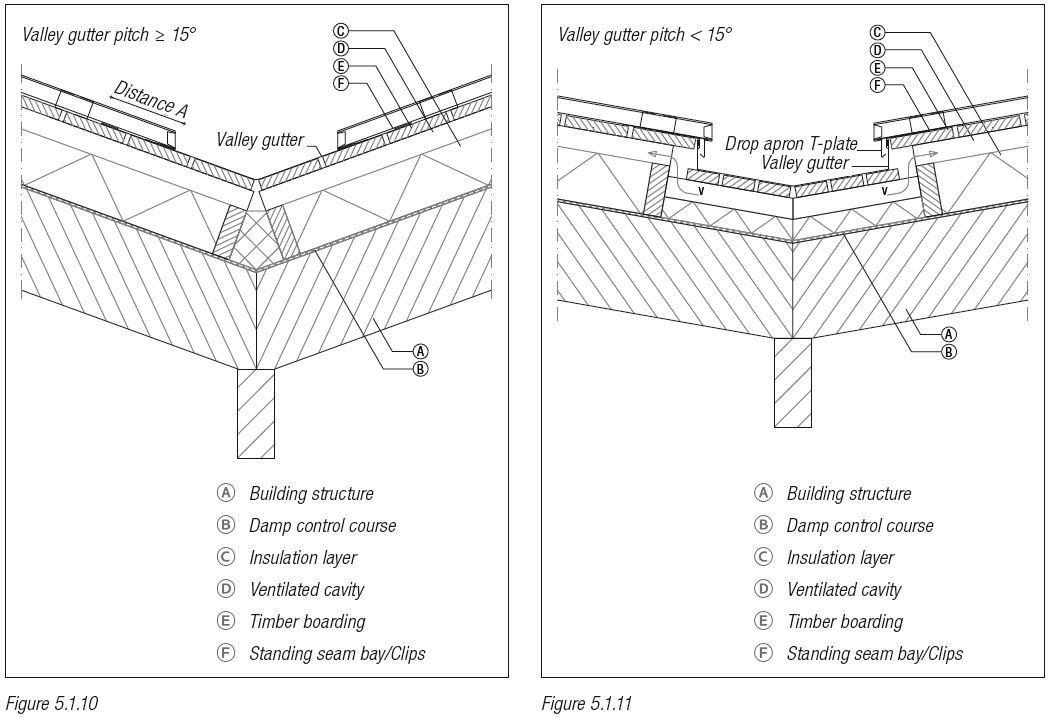
Installing the roof covering
Mark off from the axis of the roof or façade surface. The working widths are then marked off to the left and right. Consultation with the client is recommended in order to achieve the correct alignment.
Roof pitch up to 45° 5 – 10 mm
Roof pitch from 45° – 70° 5 – 50 mm
Roof pitch from 70° – 90° 5 – 100 mm
Expansion
Taking into account the expansion and contraction of the zinc as a result of temperature changes, bay lengths of up to 10 meters are recommended. If the roof length exceeds 10 meters, an expansion device is required.
The implementation of this depends on the roof pitch. The overlap is necessary in order to make the construction rainproof.
Applying the standard standing seam roof bays.
The standing seam systems are laid from left to right or vice versa, according to the markings on the boarding. Before the first bay is laid, the eave connection should be made. An example is the drop apron connection in Figure 5.1.6. The first seamed bay is laid with an overhang of at least 25 mm over the T-plate.
Because the first seamed bay has to form a side connection, it will usually not be of full width. Once the bay is hooked in, the fixed and sliding clips are applied. The position of the fixed clips depends on the roof pitch. For the distance between the clips for different bay widths and roof heights, see Table 5.1.6. After the first bay is laid and the clips fitted, the next bay is placed laterally without force and with sufficient overhang. The seams of the hooked bays are then sealed with a seaming tool or seaming machine.
Ridge Attachment
To make a ridge connection, the profiled bays are set up. The whole is covered with a ridge profile (see Figure 5.1.7).
Batten verge connection
For the verge connection, the zinc of the first and the last bay is put up against a wood roll, height at least 55 mm. These bays can be applied in the desired width. The batten verge detail is shown in Figure 5.1.8. The wood roll is covered with a profile of choice. Both the verge capping and the raised edge of the side bay are secured with 3 clips per meter.
Wall abutment
An example of a wall abutment over the full roof width is shown in Figure 5.1.9.
Here too, a ventilation opening must be provided to ensure the principle of ventilation.
Hip roll
In a hip roof connection, a hip roll forms the separation between the two roof surfaces. A capping covers the hip roll. The height of the raised edge of the standing seam against the roof batten is at least 55 mm measured perpendicular to the line of the hip roll.
Valley gutter
The valley gutter covers the enclosed corner of two roof surfaces as shown in Figure 5.1.10. The endings of the standing seam bays are cut and folded. The bays are then hooked onto the continuous strip. This continuous strip is soldered onto the roof valley gutter in lengths of, for example, 1 meter. If the roof pitch is less than 15°, a box gutter must be installed in the valley (see Figure 5.1.11).
Request free zinc standing seam system documentation and samples
Are you interested in a zinc standing seam system and would you like to receive a sample or get in touch with one of our experts? Request information, a technical advice book or a sample without obligation: